生地製造メーカー O社様にシステム開発・導入を行った事例をご紹介します。
課題と目標:手入力のデータ集計による事務員の作業時間を削減したい
【課題】 稼働状況を集計する仕組みは、編立機に据え付けているカウンターを有線でホスト機にデータ転送・集約し、データが印刷出力されるため、データ活用には事務員が手入力で再入力・集計する必要があり、作業工数やタイムラグが発生していた。
有線で設備が繋がれており、迅速な段取り変更が実施できなかった。
【目標】 収集したデータを活用するための事務員の作業(入力・集計・資料化)時間を削減する。
「非稼働時間」を「稼働時間」にすることで、10%程度の生産性向上を実現する。
課題解決:自動集計の仕組みを構築、稼働状況の可視化により最適な生産体制を実現
【自動集計の仕組みを構築】 編立機に機械の振動を感知するセンサーを取り付け子機・中継器を介してサーバ に稼働状況等のデータをリアルタイムに集約。集約されたデータを、専用ソフトウェア で自動集計される仕組みを構築。
【稼働状況の可視化により最適な生産体制を実現】 どのデータを何に活用するのかを明確化したことにより、「段取、生産、休止」の3つ の作業状態が数値とグラフでリアルタイムに可視化され、非稼働時間の発生頻度、 タイミングを把握できる為、生産予定に対する現状の把握が可能となり、管理者に よる作業者の割り当てを迅速に変更でき、最適な生産体制を構築する事ができる ようになった。
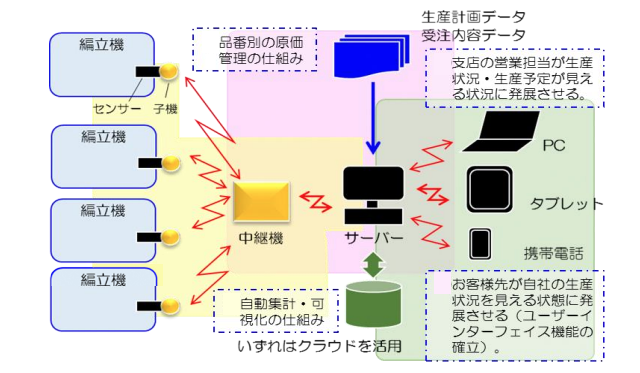
今後の展望:品番別原価管理とリアルタイムの生産状況・生産計画の可視化へと発展
【品番別の原価管理への発展】 品番別の作業時間を可視化する事で、作業に関する人件費・その他の固定費等の経費按分をすることとし、製造原価の計算を容易にする。
【営業担当者が生産状況・生産計画をリアルタイムに把握できる仕組みへ発展】 将来的には、当社の東京営業所にいる営業担当者が、客先訪問時に必要に応じて工場の生産状況や生産計画を確認し、その場で今後の受注調整等が行える環境を整える。
導入結果:事務員のデータ活用のための1日約3時間の作業がなくなり、月75時間の作業工数削減につながった。
【イニシャルコスト】約400万円(Wi-Fi環境整備、各種センサーの導入、集計ソフト開発など) 【ランニングコスト】通信費
過去にも挑戦して、費用の高さから断念した経緯がありました。しかし、近年のIT技術の進歩やITツールの普及により、柔軟で・安価で・効果的なツールを確保できました。随時、編立機以外にも普及させていきます。
Comments